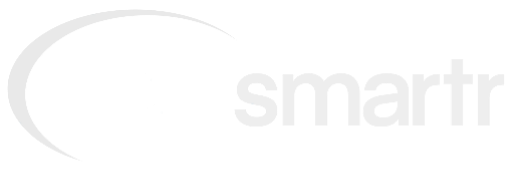
Product Packages
Join a Community of Excellence
LCEsmartr isn’t just another online platform; it’s a gateway to transform reliability and operational management. With nearly 50 years of expertise in reliability and maintenance best practices, LCEsmartr provides you with unparalleled access to a comprehensive body of knowledge. We are your trusted advisor, committed to helping you excel in operations and empower your workforce.
The LCEsmartr Promise
When you subscribe, you also gain a dedicated subject matter expert coach, guiding you in implementing improvements where they matter most.
Empowerment through Knowledge
With LCEsmartr, upskill your workforce and transition from reactive to proactive operations. We provide the tools and support you need to succeed.
Start Your Journey with LCEsmartr
Join us and elevate your operations with LCEsmartr, a revolution in reliability and operational excellence.
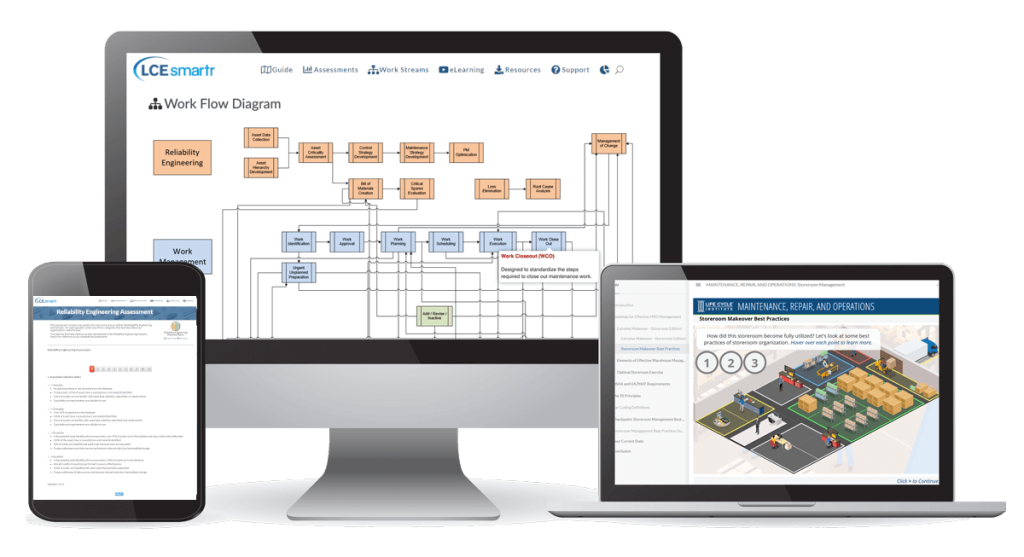
Flexible Packages
With LCEsmartr, you have the flexibility to choose the level of support that fits your current challenges and goals. Whether you need to address specific problem areas or are ready for a comprehensive transformation from reactive to proactive operations, our customizable packages provide the perfect fit.
LCEsmartr packages range from smaller enterprises to unlimited global user based packages. Contact Us to discuss pricing options with a solution expert today.
Curated for You
LCEsmartr captures reliability-centered best practices for the work streams in work process diagrams. Each work process is supported by LCEsmartr resources, including a responsibility matrix, implementation support tools and coaching card performance standards.
eLearning Courses
Our catalog of online courses integrate decades of reliability best practices, learning theory and cutting-edge eLearning design. Our training is developed by the Life Cycle Institute – LCE’s human performance practice, and integrates quizzes, action plans and downloadable resources for on-the-job application.
LCEsmartr pricing is customized to the client’s needs. Year 1 pricing is based on number of users and content selected. Annual renewal fees are a percentage of Year 1 fees.
Select a single work stream package or choose multiple work streams. Enterprise customers can add eLearning courses at any time depending on your teams’ needs.
LCE’s instructional designers can develop online training for your operations or an in-person training curriculum to develop needed competencies in your organization.
Enterprise LCEsmartr packages include a dedicated SME coach to help implement improvements and
Customize work processes and tools for your operations. Add program standards and practitioner resources to LCEsmartr to make it your reliability program portal.
Track system adoption and progress towards your program goals through our flexible business intelligence dashboards.
Processes that establish responsibility for work identification, approval, planning, scheduling and execution of work.
Processes and function responsible for risk management, loss elimination, asset care, and life cycle asset management
Processes to ensure the right materials and spare parts are available at the right time, in the right place, for the right price.
Processes and best practices that enable the organization to design, procure, construct, operate, and maintain to the lowest lifecycle cost at an acceptable level of business risk.
Processes focused on total cost of ownership, and on maximizing the ROI over the life cycle of the asset. DfR begins with the interaction of Capital Delivery and Conceptual Design, and ends with Commission and Validation processes.
Processes to improve shutdowns, starting with a 3-year plan, scoping, planning, scheduling, execution and lessons learned.
eMPS covers the entire proactive work management process, from identification through work closeout. With built-in practical application and downloadable tools, you will be able to immediately apply what you learn.
eRCM gives learners the resources, practice, and on-the-job action plans to effectively apply a risk-based reliability centered maintenance methodology and facilitate an RCM analysis.
eMRO is a toolkit of best practices for storeroom, spare parts, and inventory management. The course combines industry standards and best-practice benchmarking to help you manage your storeroom.
eRCA introduces a root cause analysis program model and 30+ downloadable resources to help teams classify problems, select the appropriate RCA tools, facilitate investigations, validate corrective actions, and prevent recurring failures.
This course highlights the strategic role of the reliability engineer and covers how to develop a reliability program centered on risk management, loss elimination, asset care, change management, and total life cycle cost.
This course integrates condition-based maintenance, predictive and other technologies into a broader asset-maintenance strategy to diagnose, prevent, and delay failures. It also provides guidance and dozens of downloadable resources to lead an effective failure avoidance program.
LCEsmartr = Your Complete Solution
Whether you’re just starting your journey or looking to refine an established program, LCEsmartr is designed to meet your operation’s unique needs. Our platform is not a one-size-fits-all solution; it’s a versatile toolset that adapts to where you are in your program’s maturity and grows with you.
Sample Package Options
Each LCEsmartr package can add upgrades, content, and additional tools at any time.
Small Team
1 - 10 Users-
Implementation Roadmap
-
1 Standard Work Package
-
1 Maturity & Reliability Assessment
-
1 Practitioner Toolkit
-
1 eLearning Course
-
Expert Coaching
-
Program Tools & Resources
Mid Sized Operation
11 - 50 Users-
Implementation Roadmap
-
3 Standard Work Packages
-
3 Maturity & Reliability Assessments
-
3 Practitioner Toolkits
-
3 eLearning Courses
-
Performance Dashboards
-
Expert Coaching
-
Program Tools & Resources
Full Scale Enterprise
> 50 Users-
Implementation Roadmap
-
3 Standard Work Packages
-
3 Maturity & Reliability Assessments
-
3 Practitioner Toolkits
-
4 eLearning Courses
-
Performance Dashboards
-
Expert Coaching
-
Program Tools & Resources
Take a tour and see all of the system's features, or reach out so we can customize a solution to meet your needs.
Challenges in Manufacturing and How LCEsmartr Playbook Solves them
Workforce Management
- Loss of experience and knowledge from retiring workforce and/or high turnover
- Difficulty onboarding new employees in reliability and asset management program standards
- Enterprise-wide lack of understanding maintenance and reliability best practices to support proactive decision-making
- No or limited standard work to support program sustainability, plants survive on “tribal knowledge”
- No or limited upskilling/reskilling program for new hires or continuing education and professional development
- Difficulty managing change, getting people to adopt a new way of operations during necessary improvement initiatives
- Inefficient, inconsistent or undefined work flows and processes causing decreased productivity, necessitating rework and creating waste
- 6+ online courses that comprise over 20 days of classroom instruction to support quick and effective onboarding, skill-building, and development
- Flexible curriculum for an enterprise-wide competency building and alignment on work management, reliability engineering, materials management, design for reliability and capital delivery best practices
- Implementation guide with templates and step-by-step instructions on how to champion and drive change
- Library with 200+ tools to support program improvement and sustainability
- Reliability SME support to identify and curate an enterprise learning program
Equipment Maintenance and Reliability
- Reactive operations in a “fix it when it breaks” mentality
- Excessive unplanned downtime and chronically bad actors
- Few or no maintenance plans based on critical equipment or failure modes
- Loss elimination and RCA programs that don’t get expected results or validate and share corrective actions
- Little to no CMMS data standards or ability to accurately turn CMMS data into actionable information and insights
- No long-term asset management planning, business needs assessments, or formal capital management processes
- Reliability Engineering program assessment to identify current state and improvement opportunities
- 11 reliability engineering processes, responsibility matrixes and coaching cards
- Program tools to support building an asset hierarchy, perform an asset criticality analysis, evaluate critical spares and developing bill of materials (BOMs)
- Templates to conduct failure mode and effects analysis (FMEA) and build RCM-based equipment maintenance plans
- Loss elimination, root cause analysis, and management of change processes and program guides
- Reliability Engineering key performance indicators and maturity levels to gauge program progress
Storeroom and Inventory Management
- An inability to identify which items should be in stock and which should be designated critical spares
- Chronic stock-outs
- Unknown inventory of obsolete stock items
- Excessive carrying costs, likely due to over-stocking and obsolete inventory
- Storeroom is poorly managed, without disciplined parts classifications or inventory cycle counting
- Maintenance personnel and crafts people rarely have the parts they need to complete a job; job kitting is not formal or standardized
- Materials Management program assessment to identify current state and improvement opportunities
- 15 storeroom management processes, responsibility matrixes and coaching cards
- Program tools to support critical spares identification and management
- Inventory management guides on cycle counting, ABC classification and obsolescence management
- Job kitting program set-up and support tools
- Key performance indicators and maturity levels to gauge program progress
Operational Efficiency
- Inability to meet customer demand – a need to increase capacity and optimize production throughput
- Low overall equipment effectiveness – sub-par asset availability, quality problems, inadequate production rates
- Operational costs are too high – Pressure to reduce costs and lean-out operations
- Assessments to determine the current state of your operations and develop plans for improvement
- Work management program tools including processes and program tools from work identification through closeout
- Loss elimination and root cause analysis program support tools to drive improvements
- Key performance indicators and maturity levels to gauge program progress
- Focus broadly across multiple sites and geographies, with everyone “playing by the same rulebook”
Storeroom and Inventory Management
- An inability to identify which items should be in stock and which should be designated critical spares
- Chronic stock-outs
- Unknown inventory of obsolete stock items
- Excessive carrying costs, likely due to over-stocking and obsolete inventory
- Storeroom is poorly managed, without disciplined parts classifications or inventory cycle counting
- Maintenance personnel and crafts people rarely have the parts they need to complete a job; job kitting is not formal or standardized
- Materials Management program assessment to identify current state and improvement opportunities
- 15 storeroom management processes, responsibility matrixes and coaching cards
- Program tools to support critical spares identification and management
- Inventory management guides on cycle counting, ABC classification and obsolescence management
- Job kitting program set-up and support tools
- Key performance indicators and maturity levels to gauge program progress
Operational Efficiency
- Inability to meet customer demand – a need to increase capacity and optimize production throughput
- Low overall equipment effectiveness – sub-par asset availability, quality problems, inadequate production rates
- Operational costs are too high – Pressure to reduce costs and lean-out operations
- Assessments to determine the current state of your operations and develop plans for improvement
- Work management program tools including processes and program tools from work identification through closeout
- Loss elimination and root cause analysis program support tools to drive improvements
- Key performance indicators and maturity levels to gauge program progress
- Focus broadly across multiple sites and geographies, with everyone “playing by the same rulebook”
Storeroom and Inventory Management
- An inability to identify which items should be in stock and which should be designated critical spares
- Chronic stock-outs
- Unknown inventory of obsolete stock items
- Excessive carrying costs, likely due to over-stocking and obsolete inventory
- Storeroom is poorly managed, without disciplined parts classifications or inventory cycle counting
- Maintenance personnel and crafts people rarely have the parts they need to complete a job; job kitting is not formal or standardized
- Materials Management program assessment to identify current state and improvement opportunities
- 15 storeroom management processes, responsibility matrixes and coaching cards
- Program tools to support critical spares identification and management
- Inventory management guides on cycle counting, ABC classification and obsolescence management
- Job kitting program set-up and support tools
- Key performance indicators and maturity levels to gauge program progress
Operational Efficiency
- Inability to meet customer demand – a need to increase capacity and optimize production throughput
- Low overall equipment effectiveness – sub-par asset availability, quality problems, inadequate production rates
- Operational costs are too high – Pressure to reduce costs and lean-out operations
- Assessments to determine the current state of your operations and develop plans for improvement
- Work management program tools including processes and program tools from work identification through closeout
- Loss elimination and root cause analysis program support tools to drive improvements
- Key performance indicators and maturity levels to gauge program progress
- Focus broadly across multiple sites and geographies, with everyone “playing by the same rulebook”